SEARCH
when you need our product,simply enter the name of the product you are looking for to continue.
Refractory Knowledge
- Manufacture of Magnesium and Aluminum Brick
- Clay refractory ramming material
- Five Advantages of Ceramic Fiber Board
- Introduction of Refractory Materials for Foreign Glass Kiln
- Ceramic Fiber Blanket Not Equal To Ceramic Fiber Felt
- Refractory Materials Used In the Bogie Hearth Furnace
- Phone:0086-371-63838939
- Email:sales@sunriserefr.com
- Office Address: No.36 Fengchan Road Of Zhengzhou, Henan, China (Mainland)
Contact Us
News & Events
Considerations for the Application of Ceramic Fiber Module
Date:2016-05-17 18:02 | From:Zhengzhou Sunrise Refractory | Author:admin
Some matters need attentions when ceramic fiber module is used as the lining, which may affect the use and economy of the lining.
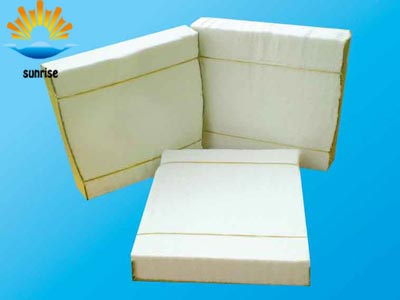
1) The materials of ceramic fiber module
As for the aspect of economic rationality, the module lining should be designed into the composite lining, which is made up of back lining as the cold surface and ceramic fiber module as the hot surface. Therefore, the selection of materials includes the selection of the hot surface module and cold lining materials. For the composite ceramic fiber lining structure, the materials should not only meet the temperature conditions but also the smoke and gas conditions as well as economic benefits, in order to achieve the best energy saving effect. The working temperature of the ceramic fiber is not only up to its chemical composition, but also the fuel, atmosphere and environment conditions.
2) The selection of density
Its bulk density has great effect on the thermal conductivity. Ceramic fiber is the mixture of solid fiber and air. Since it has high porosity, it has excellent insulation performance. Its bulk density should be with a range. The best bulk density of the module is 180-240kg/m3. If it is lower than this, its erosion resistance to smoke and gases will be reduced. If the bulk density is higher than this, the fiber is easy to break during the compressing process of the module.
3) The fiber forming process
Ceramic fiber can be divided into blown fiber and spun fiber according to its fiber forming process. Spun fiber is recommended for the ceramic fiber module, since it has longer fiber and higher tensile strength.
4) Erosion resistance to smoke and gases
The ability of the module to resist the erosion of smoke and gases decreases with the increase of temperature and the biggest is 25 m/ s. Brushing or spraying coatings on the surface can improve the erosion resistance to smoke and gases. However, the coating has different shrinkage at with ceramic fiber at high temperature, which makes the coatings crack and spall. So, coatings are not recommended. If necessary, surface hardening agents can be used.
In some devices with high sulfur content in the fuel or smoke, even if coatings are applied, the lining will still be corroded. In this case, 50-70mm lightweight castables can be used as the back lining to prevent the erosion of smoke and gases.
If you have any needs our help or are interested in our products, you can click online advisorychat with us online, or call our customer service telephone: 0086-0371-63838939. We will sincerely serve for you!