SEARCH
when you need our product,simply enter the name of the product you are looking for to continue.
Refractory Knowledge
- Ceramic Fiber Blanket Not Equal To Ceramic Fiber Felt
- Refractory Materials Used In the Bogie Hearth Furnace
- Clay refractory ramming material
- Five Advantages of Ceramic Fiber Board
- Improve the service life of chrome corundum bricks for gasifi
- Lightweight firebrick ten functions
- Phone:0086-371-63838939
- Email:sales@sunriserefr.com
- Office Address: No.36 Fengchan Road Of Zhengzhou, Henan, China (Mainland)
Contact Us
News & Events
How to Produce Ceramic Fiber by the Melting Method
Date:2015-11-19 10:46 | From:Zhengzhou Sunrise Refractory | Author:admin
Ceramic fiber is a type of light weight refractory insulation material, with advantages of low density, low thermal conductivity, good thermal malleability, easy construction, low energy consumption and high efficiency. Vitreous ceramic fiber is generally made by the melting method.
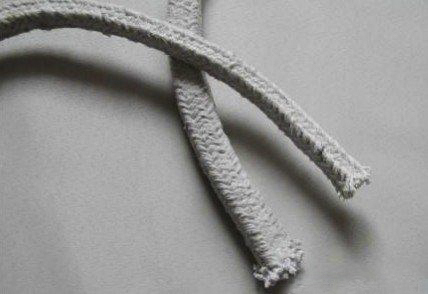
The melting method can also be divided into blowing melting method, spinning melting method and high-speed centrifugation melting method. The blowing melting method is to melt the raw material in a high temperature furnace into colloid to form a steady stream and then blow it into fiber with compressed air or steam. The spinning melting method is to melt the raw material in a high temperature furnace into colloid to form a steady stream and then spin it into fiber with a group of high-speed rotary drums. The high-speed centrifugation melting method is to melt the raw material in a high temperature furnace into colloid to form a steady stream and then spin it into fiber with a high-speed rotating disk (30000-120000r/min).
The procedure of the melting method includes 3 steps: raw material preparation, melting and fiberizing.
1) Raw material preparation
The flint clay for the production of common ceramic fiber should at least contain 45% Al2O3+SiO2, 45% Al2O3 and no more than 1.2% Fe2O3 and 0.5% Na2O+K2O. The raw materials for high purity aluminum silicate fiber and high alumina fiber are industrial pure alumina and silica, which contains more than 99% Al2O3+SiO2.
2) Melting
Since the melting points of the raw materials, the melting temperature is generally 2000 ~ 2200 ℃. The raw materials are generally melted in an electric arc furnace (EAF) or an electric resistance furnace. The electric arc furnaces can be divided into single-phase and three-phase furnaces. Since the single-phase electric arc furnace can reduce the circuit power, it has been out of use. The EAF has concentrated high-temperature region and can act as refractory insulation materials itself. When melting the raw materials in the EAF, the steam is not continuous and stable, the EAF cannot continuously operate, the quality is low and the thermal efficiency is low. Thus, it requires no water cooling and is more economic.
The principle of the electric resistance furnace is different from the electric arc furnace. It uses refractory metals molybdenum as electrodes. When working, electrode is immersed directly into the melt. The voltage drop between the electrodes is completely consumed in the melt. It melts the raw materials by the resistance heating. Since the temperature of the electric resistance furnace is high and the melting zone is large, the shell requires water cooling. The electrode can be made of molybdenum or tungsten and requires water cooling. The outflow port is generally made of molybdenum, tungsten or iridium, and protected with nitrogen, argon or other gases. It has stable production ability, high quality and low power consumption. When melting the raw materials, the stream is stable and can be adjusted, the loss of materials is less and the dust and noise is low. It can continuously work for 15-30 days and has a high degree of automation. Therefore, more and more factories produce ceramic fiber with electric resistance furnaces.
3) Fiberizing
The Production methods of ceramic fiber can be divided into blowing method and centrifugal spinning method. The blowing method is to blow the molten materials into fiber with compressed air. The molten materials are first dispersed into fine droplets with the high-speed air flow and then the fine droplets are elongated into fibers by the air flow. This method is simple and the resulting fiber is thin. But the fluctuation range of the fiber diameter is large, the fiber is short and the content of slag balls is high.it is suitable for small and medium sized factories with an annual output of 599t or less.
The centrifugal spinning method is to disperse the molten and stretch it into fiber by centrifugal force with a high-speed rotary centrifugal roller. The spun equipment is generally a three-roll structure with a fabric roll and two spun rolls. This method is characterized with large output, high fiber-forming rate, low content of slag balls and longer fiber. The drawbacks are that the device is complex and difficult to maintain and the power consumption is higher.
If you have any needs our help or are interested in our products, you can click online advisorychat with us online, or call our customer service telephone: 0086-0371-63838939. We will sincerely serve for you!